Handheld laser welding machines are revolutionizing industries by offering precision, efficiency, and flexibility in welding tasks. These devices have opened up new possibilities and improved productivity across various sectors. In this blog post, we’ll explore the innovative applications of handheld laser welding in different industries and how they are transforming operations. Whether you’re in manufacturing, automotive, aerospace, or even the medical field, handheld laser welding can provide significant benefits.
Manufacturing
Handheld Laser Welding in the Manufacturing
Precision Fabrication
laser welding is ideal for precision fabrication tasks. In industries that require high accuracy, such as electronics and microfabrication, the precision of laser welding ensures minimal material waste and high-quality joints. This technology is perfect for welding small components with intricate details.
Custom Manufacturing
The flexibility of laser welding allows for custom manufacturing processes. Whether it’s creating bespoke metal parts or modifying existing components, laser welding can handle various materials and thicknesses with ease, providing manufacturers with the versatility they need.
Automotive Industry
Handheld Laser Welding in the Automotive Industry
Body Repairs
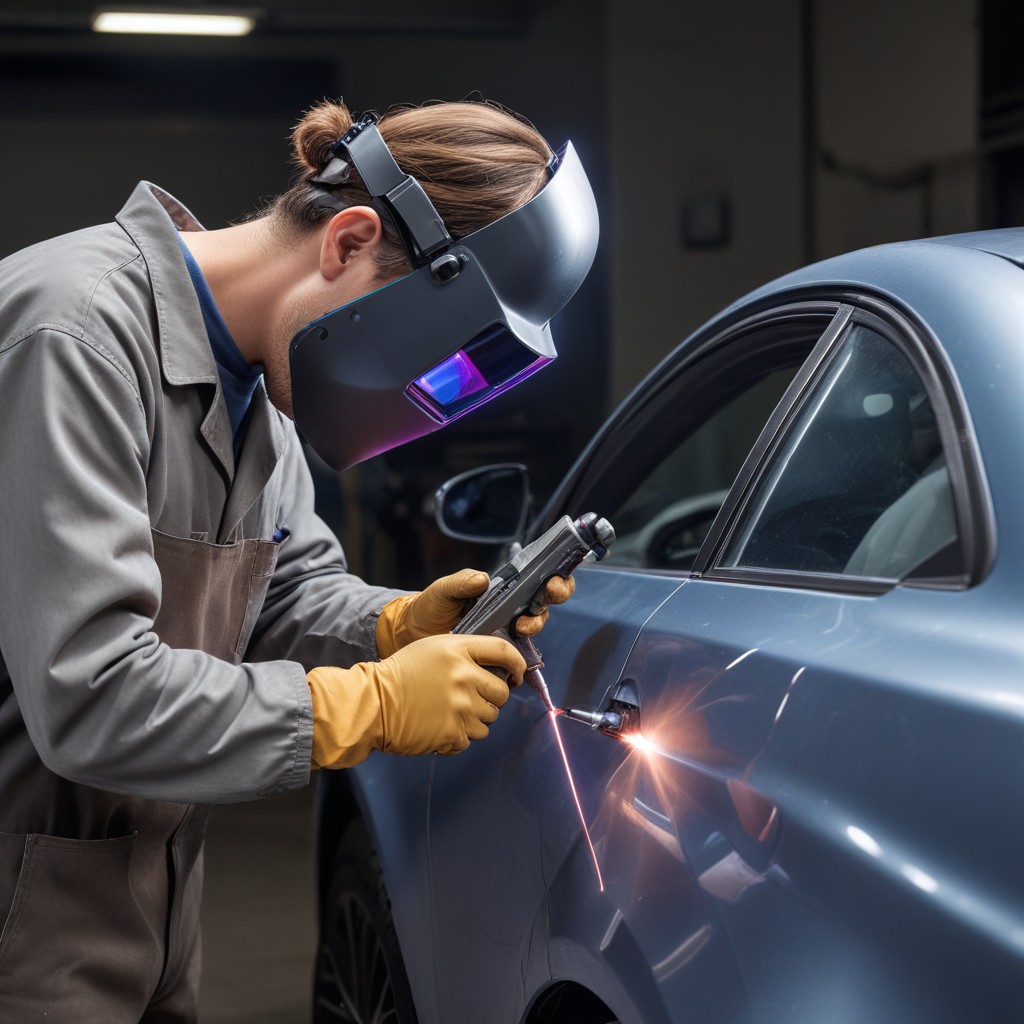
Handheld laser welding is revolutionizing body repairs and modifications in the automotive industry. Its precision enables seamless welding of different metals, resulting in strong and durable joints. This technology is particularly beneficial for repairing car bodies, where traditional welding methods might not reach or lack the necessary finesse.
Component Assembly
The automotive industry also greatly benefits from laser welding in component assembly. This technology is used to join various parts such as exhaust systems, fuel injectors, and sensors. The speed and precision of handheld laser welding enhance both the efficiency and quality of the assembly process. By quickly and accurately joining these components, laser welding significantly improves the overall production workflow in the automotive sector.
3. Aerospace
Lightweight Materials
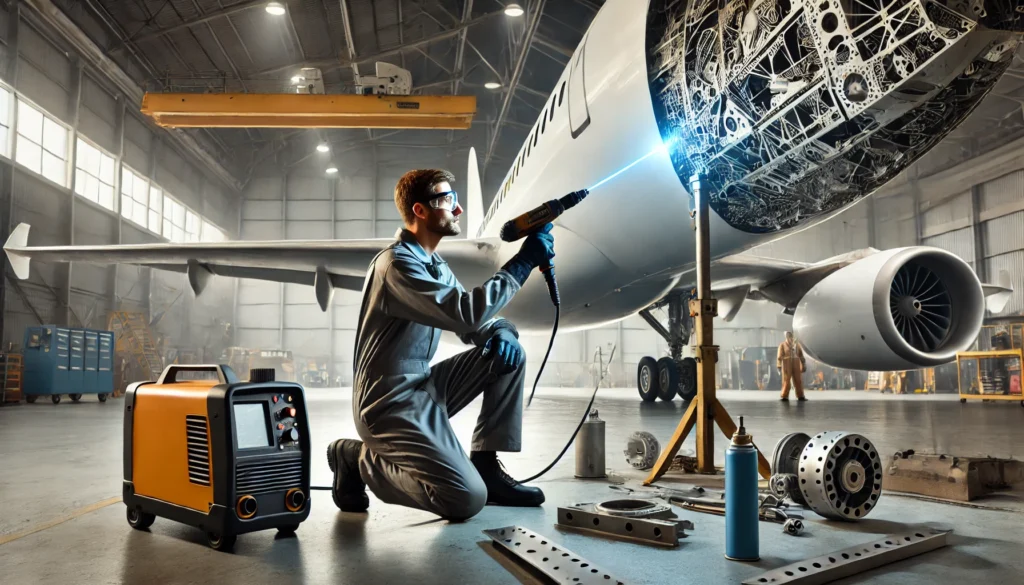
Aerospace applications require materials that are both strong and lightweight. Handheld laser welding is excellent for working with aluminum and titanium, which are commonly used in aerospace components. The technology ensures strong joints without adding excessive weight.
On-Site Repairs
The portability of laser welding machines makes them perfect for on-site repairs in aerospace. Whether it’s maintenance of aircraft components or emergency repairs, the ability to perform precise welding on the spot is invaluable.
4. Medical Devices
Surgical Instruments
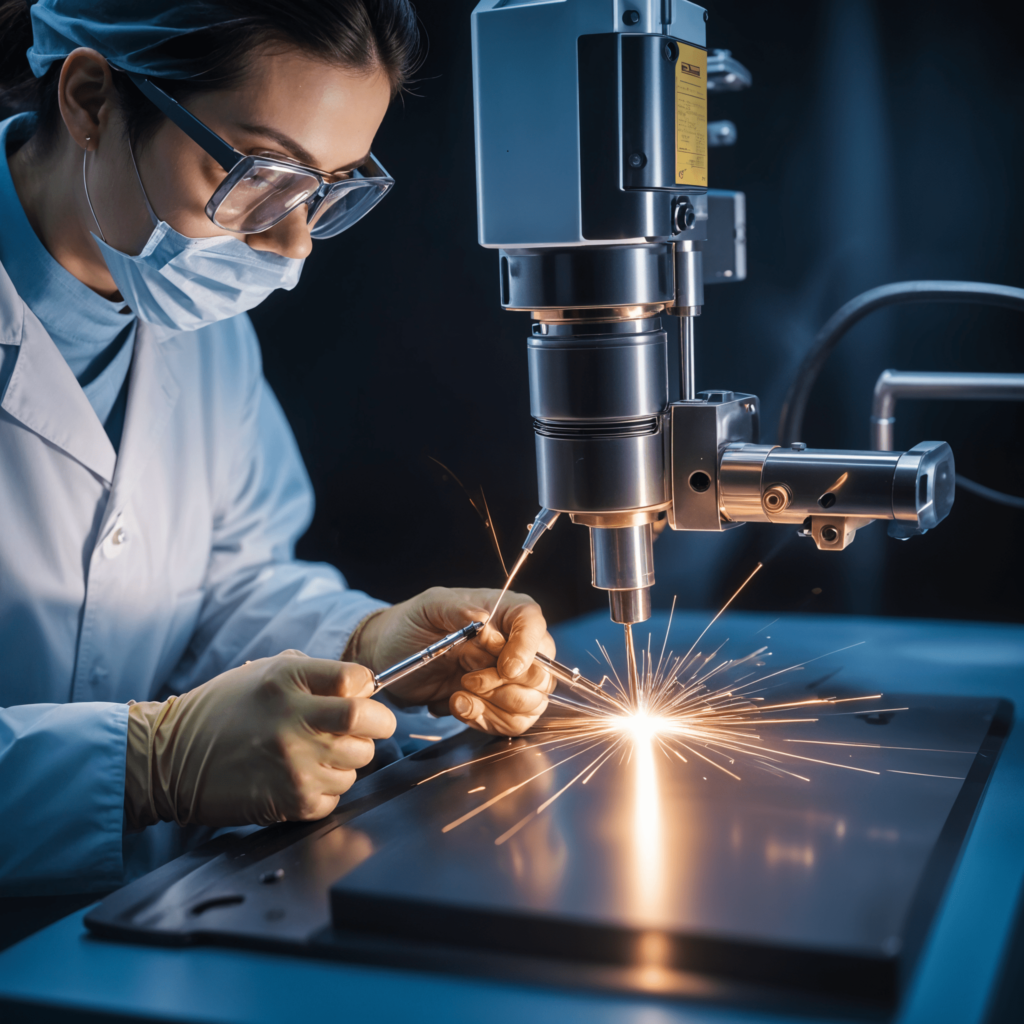
The medical device industry benefits from the precision and cleanliness of laser welding. laser welding is used to manufacture and repair surgical instruments, ensuring they meet stringent hygiene and quality standards.
Implants and Prosthetics
Creating custom implants and prosthetics requires precise and strong welds. laser welding allows for the fabrication of complex shapes and ensures biocompatibility, making it an essential tool in the medical field.
5. Jewelry and Craftsmanship
Fine Jewelry
In the jewelry industry, the precision is used to create and repair fine jewelry. It allows jewelers to work with delicate materials and intricate designs without damaging them.
Artistic Metalwork
Artisans and craftsmen use laser welding to create detailed metalwork. The precision and control offered by laser welding enable artists to bring their intricate designs to life.
Energy Sector
Pipeline Repairs
In the energy sector, particularly in oil and gas, laser welding is used for pipeline repairs. The technology allows for precise and robust welding in difficult-to-reach areas, ensuring the integrity of pipelines.
Renewable Energy
For renewable energy applications, such as wind turbines and solar panels, handheld laser welding provides the necessary precision and strength for assembling and maintaining components.
Leave a Reply